Automation Robotics
July-Aug 2025
Outline Of The Global Industrial Robotics Space
By mckinsey & Company (www.mckinsey.com)
This chapter organizes and takes stock of the current state of the global industrial robotics market and its key characteristics. The resulting overview serves as a backdrop for understanding the driving factors behind the industry’s expected growth and how it will come about.
Traditional robotics will evolve with artificial intelligents. Robotics applications and industrial manufacturing will become intelligent. Evidently Indian manufacturing has defaulted. Large scale manufacturing is going to be adopted in India. Demand; Consumption; Market; Pricing; Retal; are all in place. Robotics will become the primary ingredient for large scale manufacturing. So, dear readers of imprint automation India magazine this business opportunity is crystalized. Stay tuned. Cheers!
Overview of products and market segments
Unlike the automotive and other machinery industries, McKinsey designates industrial robotics as “low volume, high complexity.” The low-volume designation is related to the relatively small number of machines that are produced and deployed within each specification. Two realities characterize the high complexity of the industrial robotics sector: first, the breadth of different machine types that can be included under the umbrella is massive, just in the sheer number of machine types. Second, there is also great variety when it comes to the size, technology, and application areas of robots. Amid this lack of uniformity or common control systems in the robotics industry, it is important to establish a common understanding of and terminology for the scope covered before analyzing and interpreting both the end users’ and sector’s perspectives and outlook. For this whitepaper, we have leveraged McKinsey’s definitions and categorizations of industrial robots – comprising four subcategories, of which the first is further divided into four segments (see Table 1) – and automation cells and solutions (see Table 2)
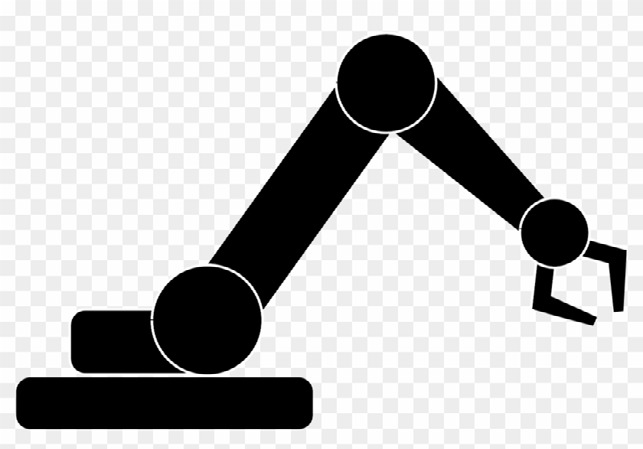
Industrial robots
Industrial robots are categorized along the lines of physical attributes (reach, weight, etc.), how they interact with humans, their mobility, and their level of autonomy.
Stand-alone industrial robots
The International Federation of Robotics (IFR) estimates that in 2017, there were around 2.1 million stand-alone industrial robots installed worldwide, with a shipment of 381,000 units globally:2
Collaborative robots
While collaborative robots are still a nascent market with about 10,000 to 20,000 units shipped in 2017, analysts expect strong future growth with more than 100,000 units to be shipped in 2020. The key difference between collaborative and standalone robots is that collaborative robots do not need safety fences for safe operations. Onboard safety mechanisms and a process design that enables collocation and collaboration allow these robots to operate directly and safely alongside human workers. These built-in safety mechanisms reduce the need for external safety measures, such as fencing and interlock for entry, thus reducing installation design costs. Collaborative robots can be simpler to apply, connect, and run. Quite often, these are single robot installations with simple and discrete input/ output interfaces that lower installation and programming costs. Collaborative robots provide an advantage wherever workers benefit from physical support – for example, by improving process ergonomics and potentially giving older workers or workers with restricted physical ability the assistance they need to be successful in manufacturing. The automotive and electronics sectors are where collaborative robots are currently deployed the most and used not only for incidental work (such as materials handling) but also for value adding (such as assembly). In logistics, however, this robotics category has application in value-added tasks (such as picking) and supportive work (such as kitting and pre-retail services).
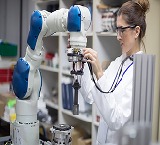
Mobile robots
Mobile robots – also known as automated guided vehicles (AGVs) – can be used in a range of applications, including warehouses and distribution centers, manufacturing intralogistics, agriculture, and other environments (especially in logistics in hospitals or retail). There are also first models and prototypes for domestic use. Expectations for AGVs are high. IFR estimates that 69,000 logistics systems had been installed in 2017 (63% of total professional service robot).
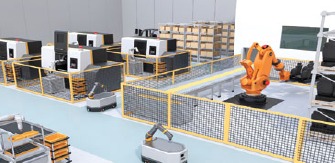
Table 1
Overview of industrial robot segments
Stand alone – articulated
Articulated robots have rotary joints and between three and six degrees of freedom enabling high flexibility (robot can bend back and forth).
Application
This is the text for the first column. You can write more about the content here.
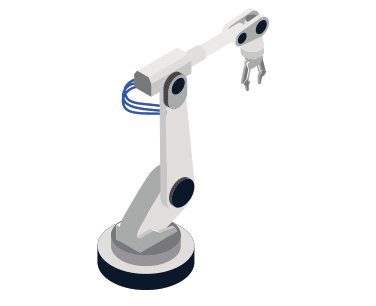
Stand alone – delta
Delta (also: parallel) robots have three arms that are connected to a base platform via universal joint Their arms are arranged as parallelograms to restrict the movement of the end platform. Actuators are located at the base platform, so that passive arms can be lightweight and move with great speed.
Application
Applications that require great precision and speed: common applications include packaging, high precision assembly, and material handling..
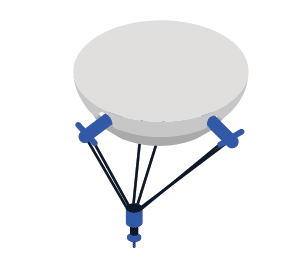
Stand alone – gantry/ linear/Cartesian
Cartesian robots consist of three axes of control that are situated at 90 degree angles of each other. The axes do not rotate but move in straight lines, which simplifies robot control linear robots are comparably simple.
Application
With no need for pedestals, Cartesian robots are useful where space is limited, as they can be mounted overhead.
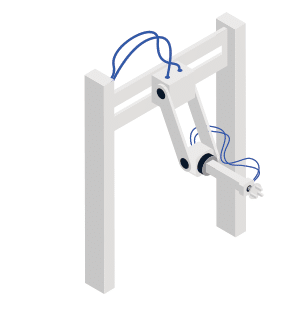
Stand alone – SCARA
SCARA robots are modelled like human arms with an elbow, shoulder, and wrist. They have three axes for x, y, and z movement and an additional axis for movement of the end effector. The setup of the axes allows the robots to extend their arm and to retract it by folding up.
Application
They are used for fast, repetitive, and precise pointto- point movements, such as palletizing, machine loading and assembly.
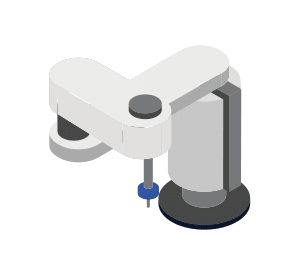
Collaborative
Collaborative robots directly interact with human workers without safety fences and are equipped with machine learning capabilities for easier programming.
Application
They are used to support human workers’ strength and precision for certain movements, in processes that require flexibility and reprogramming, or where space is limited.
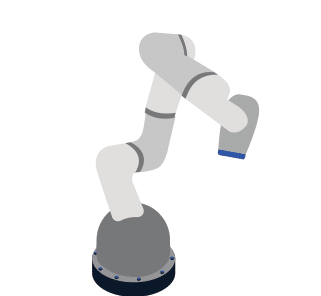
Autonomous guided vehicles (AGVs) and autonomous mobile robots (AMRs)
AGVs and AMRs are not fixedly installed but mobile. Navigation is either onboard (e.g., camera or laser based) for most advanced types or external (e.g., path based using magnetic tape, wire, or rails on the ground).
Application
Mobile robots are used for logistics and delivery as well as for moving pieces, such as boxes, pallets, or tools, in industrial settings between machinery, transfer points, or storage areas.
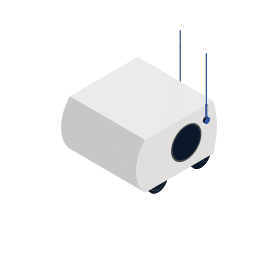
Exoskeletons
Exoskeletons are connected to the human body for support during heavy-duty or ergonomically challenging process steps. They are designed to boost the strength of human workers, e.g., increasing humans’ capacity to carry heavy weight.
Application
They can be used in industrial applications to support worker movements (e.g., lifting in warehouses).
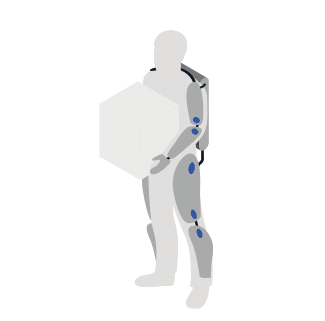
Table 2
Example of automotive production line
Exoskeletons
Exoskeletons, or human-robot hybrids, are robots connected to the human body to support heavy-duty process steps. The idea is to boost humans’ strength, increasing their capacity to carry heavy weight. Despite their potential, IFR’s estimates for this category are moderate: 6,000 powered human exoskeletons units had been sold as of 2017, and IFR forecasts that only another 48,000 units will have been sold by 2021. The technology is quite new. Currently, the primary field of applications is rehabilitation. Application areas for use of powered exoskeletons (for lower or upper extremities) have been documented by first demonstrators, and prototypes for other use cases have been tested, e.g., human performance augmentation in defense; rescue and disaster relief; ergonomic support for reducing loads on spine, hips, and shoulders when lifting heavy weights at work, particularly in logistics.
Automation cells and solutions
Industrial robots are used in an increasing variety of structures and are often employed in complete automation systems, which consist of a multitude of industrial robots. Today, individual robots are applied as a “next step” in automation, for example, for unloading a finished part from a machine tool and afterwards loading a blank part ready for processing. A “second step” in automation are production cells, where a robot has been set up for unloading and loading several machines but was designed as a cell from scratch. These cells are often subsets of full production lines and sold through integrators to the customer. Robotics OEMs offer turnkey cells, including robotic arms, delivery systems such as adhesive dispensers, cell controllers (typically PLC), and safety equipment for specific applications. The aim is to deliver a solution for the end user and reduce complexity for the end customer, who may not have the time or know-how internally. At the same time, increased standardization for the robotics OEM can lower the cost of systems through common solutions. Whether this approach will be successful remains to be seen. Solutions, often highly customer specific, include different robots and cells. Typical examples of automation solutions can be found in automotive (e.g., body in white or paint production lines). Another example is electronics, where production is highly automated and takes place in lights-out, clean-room environments.